Budayakan 6S: Siapa sangka penerapan metode sederhana ini bisa membawa perubahan besar dalam produktivitas dan efisiensi kerja? Konsep 6S, singkatan dari Seiri (Pengelompokan), Seiton (Penataan), Seisō (Pembersihan), Seiketsu (Pestandarisasi), Shitsuke (Kedisiplinan), dan ditambah Safety (Keselamatan), menawarkan pendekatan sistematis untuk menciptakan lingkungan kerja yang terorganisir, aman, dan efisien. Dari rumah tangga hingga industri manufaktur, manfaat 6S terasa nyata dalam peningkatan kualitas kerja dan hasil yang optimal.
Artikel ini akan membahas secara detail penerapan 6S, mulai dari pengertian dan tujuannya, hingga implementasi di berbagai konteks dan metode evaluasinya. Dengan pemahaman yang komprehensif, diharapkan pembaca dapat menerapkan 6S secara efektif dan merasakan manfaatnya langsung.
Pengertian dan Tujuan 6S
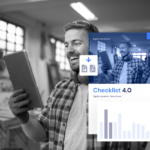
Penerapan 6S merupakan suatu metode manajemen yang efektif untuk menciptakan lingkungan kerja yang terorganisir, efisien, dan produktif. Konsep ini berfokus pada enam pilar utama yang saling berkaitan dan bertujuan untuk meminimalisir pemborosan, meningkatkan keselamatan kerja, dan pada akhirnya meningkatkan kualitas produk serta kepuasan pelanggan.
Tujuan utama penerapan 6S adalah untuk meningkatkan produktivitas dan efisiensi kerja secara signifikan. Dengan menciptakan lingkungan kerja yang bersih, rapi, dan terorganisir, waktu yang terbuang untuk mencari barang atau alat dapat diminimalisir. Selain itu, risiko kecelakaan kerja juga berkurang, sehingga meningkatkan keselamatan dan kenyamanan karyawan. Peningkatan kualitas produk juga menjadi dampak positif dari penerapan 6S karena proses kerja yang lebih terstruktur dan efisien.
Contoh Penerapan 6S di Berbagai Industri
Penerapan 6S telah terbukti efektif di berbagai sektor industri. Di industri manufaktur, misalnya, 6S diterapkan untuk mengoptimalkan tata letak pabrik, meminimalisir kerusakan mesin akibat perawatan yang buruk, dan meningkatkan efisiensi proses produksi. Di rumah sakit, 6S membantu menciptakan lingkungan yang steril dan terorganisir, sehingga mengurangi risiko infeksi dan meningkatkan kualitas pelayanan pasien. Bahkan di perkantoran, penerapan 6S dapat meningkatkan produktivitas karyawan dengan menciptakan ruang kerja yang nyaman dan efisien.
Perbandingan Kondisi Sebelum dan Sesudah Penerapan 6S
Tabel berikut ini menunjukkan perbandingan kondisi sebelum dan sesudah penerapan 6S di sebuah perusahaan manufaktur fiktif. Data ini merupakan gambaran umum dan dapat bervariasi tergantung pada konteks penerapannya.
Aspek | Sebelum 6S | Sesudah 6S |
---|---|---|
Kebersihan | Lingkungan kerja kotor dan berantakan, banyak sampah berserakan. | Lingkungan kerja bersih dan rapi, sampah terkelola dengan baik. |
Kerapihan | Alat dan bahan baku tertumpuk tidak teratur, sulit ditemukan. | Alat dan bahan baku tertata rapi dan mudah diakses. |
Keselamatan Kerja | Tinggi risiko kecelakaan kerja akibat lingkungan yang tidak aman. | Risiko kecelakaan kerja berkurang signifikan berkat lingkungan yang aman dan terorganisir. |
Efisiensi Kerja | Waktu kerja terbuang untuk mencari alat dan bahan baku. | Waktu kerja lebih efisien, produktivitas meningkat. |
Kualitas Produk | Tingkat kerusakan produk relatif tinggi. | Tingkat kerusakan produk menurun, kualitas produk meningkat. |
Poin-Penting Perencanaan Implementasi 6S
Perencanaan yang matang sangat krusial untuk keberhasilan implementasi 6S. Berikut beberapa poin penting yang perlu diperhatikan:
- Komitmen Manajemen: Dukungan penuh dari manajemen puncak sangat penting untuk memastikan keberhasilan implementasi 6S.
- Pelatihan Karyawan: Karyawan perlu dilatih dengan baik agar memahami dan menerapkan prinsip-prinsip 6S dengan benar.
- Pemilihan Tim Implementasi: Membentuk tim yang kompeten dan berdedikasi untuk memimpin proses implementasi.
- Penentuan Target dan Indikator Kinerja: Menetapkan target yang realistis dan indikator kinerja yang terukur untuk memantau kemajuan implementasi.
- Evaluasi dan Perbaikan: Melakukan evaluasi secara berkala dan melakukan perbaikan yang diperlukan untuk memastikan keberlanjutan program 6S.
Kelima Elemen 6S (Seiri, Seiton, Seisō, Seiketsu, Shitsuke)
Penerapan metode 6S, yang berasal dari Jepang, merupakan kunci untuk menciptakan lingkungan kerja yang efisien, aman, dan produktif. Kelima elemen 6S, yaitu Seiri, Seiton, Seisō, Seiketsu, dan Shitsuke, saling berkaitan dan harus diimplementasikan secara terintegrasi untuk mencapai hasil yang optimal. Pemahaman mendalam terhadap masing-masing elemen sangat penting untuk keberhasilan penerapan 6S.
Seiri (Sorting/Pengelompan)
Seiri berfokus pada pemilahan dan pengelompokan barang-barang di tempat kerja. Tujuannya adalah untuk menghilangkan barang-barang yang tidak perlu, rusak, atau jarang digunakan. Dengan demikian, ruang kerja menjadi lebih luas, bersih, dan mudah diakses. Proses ini membantu mengurangi risiko kecelakaan kerja akibat barang-barang yang berserakan.
Contoh penerapan Seiri di lingkungan kerja adalah memilah peralatan dan perlengkapan di gudang. Barang-barang yang sudah usang, rusak, atau tidak terpakai lagi dikumpulkan dan dibuang atau didaur ulang. Sedangkan barang-barang yang masih terpakai dikelompokkan berdasarkan jenis dan frekuensi penggunaannya, sehingga memudahkan pencarian dan pengambilan saat dibutuhkan. Misalnya, peralatan yang sering digunakan diletakkan di tempat yang mudah dijangkau, sementara peralatan yang jarang digunakan disimpan di tempat yang lebih terpencil.
Seiton (Setting/Penataan)
Setelah melakukan pengelompokan (Seiri), langkah selanjutnya adalah penataan (Seiton). Seiton bertujuan untuk mengatur barang-barang yang telah dipilah agar mudah ditemukan, diakses, dan digunakan. Penataan yang baik dapat meningkatkan efisiensi kerja dan mengurangi waktu yang terbuang untuk mencari barang-barang yang dibutuhkan.
Penerapan Seiton dapat dilakukan dengan menggunakan sistem penandaan, rak penyimpanan yang terorganisir, dan label yang jelas. Misalnya, di sebuah bengkel, peralatan dan perkakas dapat disusun secara sistematis di dalam laci atau rak dengan label yang menunjukkan jenis dan ukuran peralatan. Penggunaan sistem warna pada rak juga dapat membantu dalam identifikasi dan pengambilan barang yang lebih cepat. Dengan demikian, mekanik dapat dengan mudah menemukan peralatan yang dibutuhkan tanpa harus menghabiskan waktu mencari di tumpukan barang yang tidak terorganisir.
Seisō (Cleaning/Pembersihan)
Seisō menekankan pentingnya kebersihan dan pemeliharaan lingkungan kerja. Kebersihan yang terjaga akan mencegah terjadinya kecelakaan kerja, kerusakan peralatan, dan penyebaran penyakit. Seisō bukan hanya sekedar membersihkan kotoran, tetapi juga termasuk dalam pemeriksaan dan perawatan peralatan secara berkala.
Prosedur pembersihan dan pemeliharaan yang efektif dan efisien dapat dilakukan dengan membuat jadwal pembersihan rutin, menyediakan peralatan pembersihan yang memadai, dan memberikan pelatihan kepada karyawan tentang cara membersihkan dan merawat peralatan dengan benar. Misalnya, membersihkan mesin produksi setelah setiap pergantian shift, memeriksa kondisi kabel dan mesin secara berkala, dan membersihkan saluran pembuangan secara teratur.
Seiketsu (Standardization/Pestandarisasi)
Seiketsu adalah tahap dimana standar kebersihan dan penataan yang telah ditetapkan diimplementasikan secara konsisten. Hal ini penting untuk menjaga agar lingkungan kerja tetap terorganisir dan bersih dalam jangka panjang. Pestandarisasi ini mencakup pembuatan prosedur kerja standar (SOP) untuk setiap kegiatan, termasuk pembersihan dan pemeliharaan.
- Tentukan standar kebersihan dan penataan untuk setiap area kerja.
- Buatlah checklist pembersihan dan penataan yang mudah dipahami dan diikuti.
- Latih karyawan untuk mengikuti prosedur standar yang telah ditetapkan.
- Lakukan pengecekan dan evaluasi secara berkala untuk memastikan standar terjaga.
- Buatlah sistem untuk memberikan penghargaan dan sanksi bagi karyawan yang mengikuti dan tidak mengikuti standar yang telah ditetapkan.
Shitsuke (Discipline/Kedisiplinan)
Shitsuke adalah elemen terpenting dalam penerapan 6S. Ini menekankan pentingnya disiplin dan komitmen dari seluruh anggota tim untuk menjaga kebersihan, ketertiban, dan standar yang telah ditetapkan. Tanpa kedisiplinan, penerapan 6S akan sulit untuk dipertahankan dalam jangka panjang.
Untuk mencapai Shitsuke, perlu adanya kesadaran dan komitmen dari setiap individu untuk selalu mengikuti standar yang telah ditetapkan. Hal ini dapat dicapai melalui pelatihan, sosialisasi, dan penegakan disiplin yang konsisten. Sistem reward dan punishment yang adil dan transparan juga penting untuk memotivasi karyawan untuk selalu menjaga kebersihan dan ketertiban di tempat kerja.
Implementasi 6S dalam Berbagai Konteks
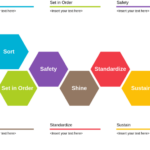
Penerapan prinsip 6S (Seiri, Seiton, Seisō, Seiketsu, Shitsuke, dan Safety) bukan hanya terbatas pada lingkungan industri. Konsep ini dapat diadaptasi dan diimplementasikan di berbagai konteks, mulai dari rumah tangga hingga lingkungan kerja yang kompleks, demi meningkatkan efisiensi, produktivitas, dan keselamatan.
Penerapan 6S di Lingkungan Rumah Tangga
Di rumah, penerapan 6S dapat menciptakan lingkungan hidup yang lebih nyaman, teratur, dan efisien. Konsep ini dapat disederhanakan dan disesuaikan dengan skala rumah tangga.
- Seiri (Mengurutkan): Membersihkan barang-barang yang tidak terpakai dan menyumbat ruang.
- Seiton (Merapikan): Menyusun barang-barang yang terpakai secara sistematis dan mudah diakses.
- Seisō (Membersihkan): Membersihkan rumah secara teratur untuk mencegah penumpukan kotoran dan debu.
- Seiketsu (Membersihkan Standar): Menjaga kebersihan dan kerapian rumah dengan menetapkan standar kebersihan dan prosedur pembersihan rutin.
- Shitsuke (Kedisiplinan): Menjadikan kebiasaan menjaga kebersihan dan kerapian sebagai bagian dari rutinitas sehari-hari.
- Safety (Keselamatan): Memastikan lingkungan rumah aman dari bahaya seperti kabel yang berserakan atau barang-barang yang mudah pecah.
Strategi Implementasi 6S di Sebuah Kantor Kecil
Implementasi 6S di kantor kecil membutuhkan perencanaan yang matang dan partisipasi aktif dari seluruh karyawan. Berikut strategi yang dapat diterapkan:
- Tahap Perencanaan: Tentukan area fokus, bentuk tim implementasi, dan jadwal pelaksanaan.
- Tahap Pelaksanaan: Lakukan penerapan 6S secara bertahap, mulai dari area yang paling bermasalah.
- Tahap Monitoring dan Evaluasi: Pantau kemajuan pelaksanaan dan lakukan evaluasi secara berkala untuk melakukan penyesuaian.
- Tahap Pemeliharaan: Pastikan kebiasaan 6S terus dijalankan dan menjadi budaya kerja di kantor.
Tantangan Penerapan 6S di Lingkungan Industri Manufaktur
Lingkungan industri manufaktur memiliki tantangan unik dalam penerapan 6S. Skala operasi yang besar, kompleksitas mesin dan peralatan, serta potensi bahaya yang lebih tinggi memerlukan strategi yang lebih terstruktur dan komprehensif.
- Perlawanan Perubahan: Karyawan mungkin enggan mengubah kebiasaan kerja yang sudah mapan.
- Biaya Implementasi: Membutuhkan investasi dalam peralatan dan pelatihan.
- Pengawasan dan Pemeliharaan: Membutuhkan pengawasan yang ketat untuk memastikan penerapan 6S berjalan efektif dan berkelanjutan.
- Keselamatan Kerja: Penerapan 6S harus diintegrasikan dengan standar keselamatan kerja yang ketat.
Penerapan 6S dalam Pengelolaan Dokumen Digital
Prinsip 6S juga dapat diterapkan dalam pengelolaan dokumen digital untuk meningkatkan efisiensi dan produktivitas.
- Seiri (Mengurutkan): Menghapus file yang tidak terpakai atau duplikat.
- Seiton (Merapikan): Mengorganisir file ke dalam folder dan subfolder yang terstruktur.
- Seisō (Membersihkan): Memeriksa dan menghapus file yang rusak atau tidak berfungsi.
- Seiketsu (Membersihkan Standar): Menetapkan standar penamaan file dan sistem pengarsipan.
- Shitsuke (Kedisiplinan): Menjaga konsistensi dalam penerapan standar pengelolaan dokumen digital.
- Safety (Keselamatan): Melindungi dokumen digital dari akses yang tidak sah dan kehilangan data melalui backup dan enkripsi.
Manfaat Penerapan 6S dalam Meningkatkan Keselamatan Kerja
Penerapan 6S secara konsisten berkontribusi signifikan pada peningkatan keselamatan kerja. Lingkungan kerja yang terorganisir, bersih, dan rapi mengurangi risiko kecelakaan kerja. Contohnya, penyimpanan bahan berbahaya yang terorganisir mengurangi risiko tumpahan atau kebakaran. Peralatan dan mesin yang terawat dengan baik mengurangi risiko kerusakan atau malfungsi. Penerapan prinsip safety secara khusus mengarah pada identifikasi dan mitigasi potensi bahaya di tempat kerja.
Alat dan Metode Pendukung 6S
Penerapan 6S yang efektif membutuhkan lebih dari sekadar komitmen; perlu didukung oleh alat dan metode yang tepat. Alat-alat ini membantu dalam proses visualisasi, pemantauan, dan pemeliharaan standar 6S, memastikan keberlanjutannya dalam jangka panjang. Berikut ini beberapa penjelasan lebih lanjut mengenai alat dan metode yang dapat digunakan.
Contoh Alat dan Teknologi Pendukung 6S
Berbagai alat dan teknologi dapat membantu mempermudah dan meningkatkan efektivitas penerapan 6S. Mulai dari yang sederhana hingga yang berbasis teknologi, semuanya berperan penting dalam mencapai tujuan 6S.
- Checklist digital: Aplikasi mobile atau software berbasis web memudahkan pembuatan, pengisian, dan monitoring checklist 6S secara real-time. Data tersimpan terpusat dan dapat diakses oleh semua pihak yang berkepentingan.
- Sistem manajemen visual: Penggunaan papan informasi digital atau fisik (seperti kanban) untuk menampilkan data kinerja 6S, target, dan progress secara visual. Ini membantu tim untuk melihat secara langsung status penerapan 6S dan mengidentifikasi area yang perlu perbaikan.
- Software manajemen fasilitas: Software ini membantu dalam manajemen aset, pemeliharaan peralatan, dan penjadwalan perawatan preventif, mendukung aspek Seiri (Sorting) dan Seiso (Shine) dalam 6S.
- Barcode scanner dan RFID: Memudahkan pelacakan barang dan peralatan, membantu dalam proses identifikasi dan manajemen inventaris (Seiri).
Langkah-langkah Membuat Checklist 6S yang Efektif
Checklist 6S yang efektif harus komprehensif, mudah dipahami, dan mudah digunakan. Berikut langkah-langkah pembuatannya:
- Tentukan ruang lingkup: Tentukan area yang akan dievaluasi dengan checklist 6S. Misalnya, area produksi, gudang, atau kantor.
- Identifikasi item checklist: Buat daftar poin pemeriksaan untuk setiap elemen 6S (Seiri, Seiton, Seiso, Seiketsu, Shitsuke, dan Safety). Pastikan poin-poin tersebut spesifik dan terukur.
- Tentukan skala penilaian: Tentukan skala penilaian untuk setiap item checklist, misalnya skala Likert (1-5) atau Ya/Tidak. Ini memudahkan dalam pengukuran dan monitoring.
- Buat format checklist: Desain checklist yang mudah dibaca dan diisi. Gunakan format tabel atau bentuk lain yang mudah dipahami.
- Uji coba dan revisi: Uji coba checklist pada area yang ditentukan dan lakukan revisi jika diperlukan untuk meningkatkan keefektifannya.
Penerapan 5S dan Peningkatan Visualisasi Tempat Kerja
Penerapan 5S (Seiri, Seiton, Seiso, Seiketsu, Shitsuke) secara signifikan meningkatkan visualisasi tempat kerja. Contohnya, penerapan Seiri (Sorting) akan menghilangkan barang-barang yang tidak diperlukan, sehingga area kerja menjadi lebih bersih dan tertata. Seiton (Set in Order) akan menempatkan barang-barang yang diperlukan di tempat yang mudah diakses dan terlihat, sehingga memudahkan pencarian dan pengambilan barang. Seiso (Shine) memastikan kebersihan dan kerapian area kerja, memberikan kesan profesional dan efisien.
Gabungan ketiga hal tersebut menghasilkan tempat kerja yang rapi, bersih, dan mudah dipahami, sehingga risiko kecelakaan kerja dan kesalahan proses dapat diminimalisir. Tempat kerja yang terorganisir secara visual juga meningkatkan efisiensi dan produktivitas.
Metode Visualisasi Data untuk Memantau Kemajuan Penerapan 6S
Visualisasi data sangat penting untuk memantau kemajuan penerapan 6S. Berbagai metode dapat digunakan untuk menampilkan data secara efektif.
Metode | Keunggulan | Kekurangan |
---|---|---|
Grafik batang | Mudah dipahami, membandingkan data antar kategori | Kurang efektif untuk data yang banyak atau kompleks |
Grafik garis | Menunjukkan tren perubahan data seiring waktu | Sulit untuk membandingkan banyak kategori sekaligus |
Diagram Pareto | Mengidentifikasi masalah utama yang berkontribusi pada sebagian besar masalah | Membutuhkan data yang cukup untuk analisis yang bermakna |
Dashboard | Menampilkan berbagai metrik 6S secara ringkas dan terintegrasi | Membutuhkan desain yang baik untuk menghindari informasi yang berlebihan |
Tips dan Trik Mempertahankan Keberlanjutan Penerapan 6S
Keberhasilan penerapan 6S bergantung pada pemeliharaan dan komitmen jangka panjang. Berikut beberapa tips untuk mempertahankan keberlanjutannya:
- Komunikasi yang konsisten: Komunikasi rutin tentang pentingnya 6S dan kemajuan yang telah dicapai sangat penting untuk menjaga motivasi dan komitmen tim.
- Pengakuan dan penghargaan: Berikan pengakuan dan penghargaan kepada individu atau tim yang berkontribusi pada keberhasilan penerapan 6S.
- Pembaruan dan revisi rutin: Tinjau dan perbarui standar 6S secara berkala untuk memastikan relevansi dan efektivitasnya.
- Pelatihan dan pengembangan: Berikan pelatihan dan pengembangan yang berkelanjutan kepada karyawan untuk memastikan pemahaman dan penerapan 6S yang konsisten.
- Integrasi dengan sistem manajemen lainnya: Integrasikan penerapan 6S dengan sistem manajemen lainnya, seperti sistem manajemen kualitas atau sistem manajemen lingkungan, untuk meningkatkan efektivitas secara keseluruhan.
Pengukuran dan Evaluasi Efektivitas 6S
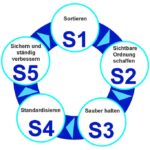
Penerapan 6S yang efektif tidak hanya berhenti pada implementasi, tetapi juga memerlukan pengukuran dan evaluasi berkelanjutan untuk memastikan keberhasilan dan keberlanjutannya. Proses ini membantu mengidentifikasi area yang perlu ditingkatkan dan memastikan bahwa upaya yang telah dilakukan memberikan hasil yang optimal. Dengan melakukan pengukuran dan evaluasi, perusahaan dapat memantau kemajuan, mengukur dampak 6S terhadap kinerja, dan membuat penyesuaian yang diperlukan.
Indikator Kunci Kinerja (KPI) untuk 6S
Pemilihan Indikator Kunci Kinerja (KPI) yang tepat sangat penting untuk mengukur keberhasilan penerapan 6S. KPI ini harus terukur, relevan, dan dapat dicapai. Berikut beberapa contoh KPI yang dapat digunakan:
- Persentase penurunan waktu pencarian barang.
- Persentase peningkatan efisiensi produksi.
- Persentase penurunan kecelakaan kerja.
- Tingkat kepatuhan karyawan terhadap standar 6S.
- Pengurangan biaya operasional akibat penerapan 6S.
Contoh Laporan Evaluasi Penerapan 6S
Laporan evaluasi 6S yang komprehensif mencakup data kuantitatif dan kualitatif. Data kuantitatif dapat berupa angka-angka yang terukur seperti persentase peningkatan efisiensi atau pengurangan limbah. Sementara data kualitatif dapat berupa umpan balik dari karyawan, hasil observasi, dan dokumentasi foto. Berikut contoh struktur laporan:
Aspek 6S | Data Kuantitatif | Data Kualitatif |
---|---|---|
Seiri (Sorting) | Pengurangan barang tidak terpakai sebesar 25% | Karyawan lebih mudah menemukan barang yang dibutuhkan |
Seiton (Set in Order) | Waktu pencarian barang berkurang 10 menit per hari | Tata letak area kerja lebih rapi dan terorganisir |
Seiso (Shine) | Penurunan insiden kecelakaan kerja sebesar 15% | Lingkungan kerja lebih bersih dan aman |
Seiketsu (Standardization) | Peningkatan konsistensi proses kerja sebesar 20% | Prosedur kerja yang lebih jelas dan mudah dipahami |
Shitsuke (Sustain) | Tingkat kepatuhan karyawan terhadap standar 6S sebesar 90% | Komitmen karyawan dalam menjaga kebersihan dan ketertiban |
Testimoni Perusahaan yang Berhasil Menerapkan 6S
“Sejak menerapkan 6S, produktivitas kami meningkat secara signifikan, dan lingkungan kerja menjadi lebih aman dan nyaman. Kami juga melihat penurunan biaya operasional yang cukup besar.”PT. Maju Jaya
Audit 6S Berkala untuk Keberlanjutan, Budayakan 6s
Audit 6S berkala sangat penting untuk memastikan keberlanjutan penerapan 6S. Audit ini dapat dilakukan secara internal atau eksternal, dan harus mencakup semua aspek 6S. Frekuensi audit dapat disesuaikan dengan kebutuhan, namun disarankan dilakukan minimal setiap tiga bulan sekali. Hasil audit digunakan sebagai dasar untuk perbaikan dan peningkatan berkelanjutan.
Proses Evaluasi dan Perbaikan Penerapan 6S
Proses evaluasi dan perbaikan penerapan 6S dapat digambarkan melalui diagram alur berikut:
- Tahap 1: Pengumpulan Data: Data dikumpulkan melalui observasi langsung, wawancara dengan karyawan, dan review dokumen.
- Tahap 2: Analisis Data: Data dianalisis untuk mengidentifikasi kekuatan dan kelemahan penerapan 6S.
- Tahap 3: Identifikasi Masalah: Masalah yang diidentifikasi kemudian diprioritaskan berdasarkan dampak dan urgensi.
- Tahap 4: Perencanaan Perbaikan: Rencana perbaikan disusun untuk mengatasi masalah yang telah diidentifikasi.
- Tahap 5: Implementasi Perbaikan: Rencana perbaikan diimplementasikan dan dipantau pelaksanaannya.
- Tahap 6: Evaluasi Hasil Perbaikan: Hasil perbaikan dievaluasi untuk mengukur efektivitasnya.
- Tahap 7: Dokumentasi: Semua proses dan hasil evaluasi didokumentasikan dengan baik.
Pemungkas: Budayakan 6s
Penerapan 6S bukanlah sekadar tren, melainkan investasi jangka panjang untuk peningkatan produktivitas dan efisiensi. Dengan konsistensi dan komitmen dari seluruh anggota tim, 6S akan menciptakan budaya kerja yang lebih baik, meningkatkan keselamatan kerja, dan menghasilkan lingkungan yang lebih produktif. Mulailah dengan langkah kecil, evaluasi secara berkala, dan nikmati transformasi positif yang akan dirasakan di lingkungan kerja Anda.